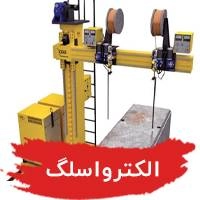
چکیده
جوش کاری الکترواسلگ چیست؟
فرآیند جوشکاری الکترو اسلگ ( Electro slag welding ) که به فارسی " جوشکاری سرباره الکتریکی " ترجمه شده است، حدود 60 سال پیش توسط یکی از محققین انستیتو جوش پاتون در کشور روسیه به ثبت رسید. علیرغم سابقه و کاربرد زیاد این فرآیند جوشکاری در دنیا، در حال حاضر این فرآیند کاربرد کمی در صنایع ایران دارد. این فرآیند جوشکاری به طور کلی بهعنوان روشی جهت اتصال مقاطع خیلی ضخیم بهصورت جوش سربالا و در یک پاس شناخته میشود و جوشکاری مقاطع غیر قابل دسترسی که با فرآیندهای جوشکاری قوسی معمولی امکان جوشکاری آن غیر ممکن و یا به سختی امکانپذیر است را فراهم مینماید. بهعنوان مثال، جوشکاری استیفنر داخل باکس به دیواره باکس.
جوش کاری الکترواسلگ چیست ؟
اصول فرآیند :
در فرآیند جوشکاری سرباره الکتریکی در نتیجه ذوب الکترود و لبههای قطعه کار، فلز جوش تولید میشود و این فلز جوش که توسط سرباره مذاب محافظت میشود درز اتصال بین دو قطعه را پر میکند.
این فرآیند با قوس الکتریکی شروع میشود. حرارت قوس باعث ذوب شدن فلاکس (پودر) میشود و سرباره مذاب بهوجود میآید. در ادامه قوس الکتریکی خاموش شده و حرارت مورد نیاز جوشکاری به وسیله مقاومت الکتریکی سرباره مذاب که جریان جوشکاری از آن عبور می کند بهوجود میآید.
در این فرآیند معمولا شیار بین دو قطعه بهصورت شیار مربعی است که در وضعیت سر بالا قرارداده میشود و معمولاً نیازی به حرکت قطعه کار نسبت به هد جوشکاری نیست. این فرآیند بهصورت ماشینی است و وقتی شروع میشود تا انتها ادامه مییابد. با توجه به اینکه در طول فرآیند قوسی نداریم بنابراین فرآیند بدون صدا و پاشش مذاب میباشد. نرخ رسوب زیاد باعث میشود که بتوان اتصالات باضخامت زیاد را در تنها یک پاس جوشکاری و تکمیل نمود. کیفیت جوش با این فرآیند بسیار مناسب بوده ، همچنین تابیدگی زاویهای هم در این فرآیند نداریم.
همانطور که گفته شد این فرآیند با برقراری قوس الکتریکی بین نوک الکترود و انتهای درز اتصال شروع میشود. در اثر حرارت ناشی از قوس الکتریکی فلاکس (پودر) ذوب می شود. به سرعت یک لایه سرباره مذاب ایجاد میشود و قوس الکتریکی قطع میشود و جریان جوشکاری از الکترود به درون سرباره مذاب هدایت میشود. حرارت ایجاد شده در اثر مقاومت الکتریکی سرباره مذاب به اندازهای هست که الکترود و لبههای کار را ذوب کند.
مجموع الکترود و لبه قطعه کار ذوب شده فلز جوش را میسازد که با پیشرفت جوشکاری به سمت بالا تبدیل به فلز جامد میشود. این فرآیند بهصورت مستمر ادامه می یابد و همواره فلز جوش مذاب روی فلز جوش جامد قرار دارد و بر روی آن هم سرباره مذاب وجود دارد.
انواع روش کار:
دو روش اصلی برای جوش سرباره الکتریکی وجود دارد. در روش اول از یک مفتول الکترود(Wire Electrode ) و یک نازل غیر مصرفی استفاده میشود که الکترود به تنهایی وارد فلاکس مذاب شده و ذوب میشود. به این روش "روش معمولی" یاConventional Method گفته میشود.
روش دوم شبیه روش اول است با این تفاوت که نازل هم مصرف شونده است و همراه الکترود وارد فلاکس مذاب میشود به این روش "نازل مصرف شونده " یاConsumable Guide Method میگویند. در روش اول هد جوشکاری بهصورت عمودی همراه با بالا آمدن حوضچه مذاب به بالا حرکت میکند اما در روش نازل مصرف شونده هد جوشکاری ثابت بالای قطعه (حوضچه مذاب) قرار میگیرد و هر دو الکترود و نازل با بالا آمدن فلز جوش و سرباره مذاب، ذوب میشوند.
فرآیند جوشکاری سرباره الکتریکی با تکنیک نازل مصرف شونده:
در این فرآیند فلز جوش شامل الکترود و نازل مصرف شونده میباشد. مفتول الکترود به همراه نازل تا انتها وارد درز بین دو قطعه میشود. جریان جوشکاری از درون مفتول الکترود و نازل عبور میکند.در این فرآیند نیازی به حرکت هد جوشکاری در زمان جوشکاری نیست. کفشکهای نگهدارنده حوضچه مذاب بین دو قطعه میتواند حالتهای مختلفی داشته باشد. جنس کفشکها میتواند مسی با سیستم آبگرد باشد که یا به اندازه طول درز اتصال هستند و یا به صورتی هستند که بهصورت مقطعی حوضچه مذاب را نگه داشته و همراه حرکت عمودی حوضچه مذاب به سمت بالا حرکت میکنند. حالت دیگر این است که کفشکها از جنس فلز پایه هستند که در حقیقت به صورت پشت بند(Backing) عمل میکنند و در نتیجه حرارت جوشکاری ذوب شده و متصل به دو قطعه میشوند که در صورت نیاز پس از اتمام جوشکاری برداشته میشوند و یا سر جای خود باقی میمانند.
همانطور که فرآیند جوشکاری پیش میرود فلز مذاب بههمراه سرباره مذاب به سمت بالا حرکت میکنند و الکترود و نازل ذوب میشوند. نازل مصرف شونده تقریباً حدود 5 تا 15 درصد حجم جوش را تشکیل میدهد. با توجه به اینکه نازل حامل جریان جوشکاری است بایستی از دیوارههای اتصال عایق شود. با استفاده از یک پوشش عایق بر روی نازل که این پوشش در ایجاد سرباره مذاب هم کمک میکند میتوان این کار را انجام داد.
مزایا و محدودیتها:
فرآیند جوشکاری سرباره الکتریکی اغلب برای اتصالات مقاطع ضخیم در وضعیت سربالا کاربرد دارد. یکی از مزایای بسیار خوب این فرآیند هزینه تمام شده کم آن میباشد. این فرآیند همچنین نسبت به فرآیندهای جوشکاری قوسی مثل جوش زیرپودری اقتصادیتر میباشد بهخصوص در مقاطع ضخیم.
مزایای این روش را میتوان بهصورت موارد زیر بیان نمود:
1) نرخ رسوب بالا تا حدود 20 کیلوگرم در ساعت
2) قابلیت جوشکاری مقاطع ضخیم تنها در یک پاس
3) عدم نیاز به پیش گرمایی حتی در مقاطع ضخیم
4) کیفیت جوش خیلی بالا
5) حداقل نیاز به آمادهسازی لبهها
6) فرآیند کاملاً اتوماتیک با کمترین میزان خستگی اپراتور
7)بدون نیاز به حرکت قطعه در حین کار
8) عدم وجود پاشش مذاب
9) مصرف فلاکس (پودر) بسیار کم در حدود 1 کیلوگرم به ازای هر 30 کیکوگرم جوش
10) حداقل زمان جوشکاری.
محدودیتهای این روش را میتوان بهصورت موارد زیر بیان نمود:
1) این فرآیند جوشکاری فقط برای فولادهای کربنی، کم آلیاژ و بعضی از فولادهای زنگ نزن کاربرد دارد.
2)قطعه کار حتماً بایستی در وضعیت سربالا قرار گیرد.
3) بعد از شروع جوشکاری بایستی تا انتها ادامه یابد و عیوب احتمالی گریز ناپذیر است.
4) این فرآیند برای ضخامتهای کمتر از 15 میلیمتر کاربرد ندارد.
5) جوشکاری قطعات با شکل پیچیده خیلی مشکل و یا شاید غیر ممکن باشد.
مواد مصرفی جوشکاری:
-
مواد مصرفی در فرآیند جوشکاری الکترواسلگ با نازل مصرف شونده شامل مفتول الکترود، فلاکس و نازل مصرف شونده میباشد.
الکترود:
-
الکترودهای مورد استفاده به دو صورت توپر و توپودری قابل کاربرد هستند. سایزهای قابل استفاده 1.6 ، 2، 2.4 ، 3.2 و 4 میلیمتر میباشد که سایز 3.2 میلیمتر کاربرد بیشتری دارد. الکترودهای مورد استفاده برای جوش زیرپودری را میتوان برای این فرآیند به کار برد.
فلاکس( پودر ):
فلاکس جوشکاری نقش مهمی در این فرآیند بر عهده دارد هر چند که مصرف کمی دارد. در طی فرآیند جوشکاری فلاکس علاوه بر محافظت از حوضچه مذاب نقشهای مهم دیگری را نیز دارا میباشد. با توجه به اینکه حرارت مورد نیاز جوشکاری ناشی از مقاوت الکتریکی سرباره مذاب میباشد، میزان هدایت الکتریکی سرباره مذاب (فلاکس) تأثیر زیادی در این فرآیند دارد. اگر هدایت الکتریکی فلاکس مذاب خیلی زیاد و مقاومت الکتریکی آن کم باشد، در نتیجه بین نوک الکترود و سطح سرباره مذاب قوس الکتریکی بهوجود میآید و اگر مقاومت الکتریکی سرباره خیلی زیاد و هدایت الکتریکی آن خیلی کم باشد جریان قطع شده و جوشکاری متوقف میشود.
همچنین سیالیت سرباره مذاب باید به اندازه کافی باشد تا با گردش آن حرارت به خوبی در کل درز اتصال توزیع شود. در صورتی که سرباره مذاب سیالیت کمی داشته باشد، عیب ناخالصی سرباره(Slag Inclusion) در جوش بهوجود میآید و اگر سرباره مذاب سیالیت زیادی داشته باشد، سرباره در فضاهای کوچک بین قطعه کار و کفشک نفوذ پیدا کرده و حبس میشود.
در طی فرآیند مقدار کمی پودر (فلاکس) مصرف میشود. در شروع فرآیند مقدار کمی پودر جهت شروع نیاز میباشد.در طی فرآیند مقداری از فلاکس بین کفشکها و دو سمت جوش باقی میماند که بنابراین لازم است در طی فرآیند مقدار کمی پودر جهت جبران کم شده ارتفاع سرباره اضافه شود.